Route Creations - D365 - Microsoft Dynamic Supply Chain Management (Production Control). Manufacturing MB320
Route:
A route defines the structure of the production process. In other words, it
defines the order of operations.
Basic
Setup for Route:
- Create Route: A route describes the order of operations that
is used to produce a product or product variant. (Mentioned below).
- Route version: Here you can create different route version –
i.e., Based on Different site 2 or 3, from different date range 2/2- 22/5/2023
for Qty 50 or 60. (So if you have order for more than 50 Qty for site 2 then this
route version will be picked)
- Operations: An
operation is a step in the production process. Assembly,Cutting etc .
- Run Time : what amount of time will above operation take
to produce this process Qty. Example 8 hours
- Process Qty : Total
Qty that will be produced after the operation based on Run time. Example 20 Qty
- Next = if the Value is 0 that means we are ending the operation but if its more then 1 then the new Operation will be there to produce the Goods.
- Route Group : Every operation can be further broken down into Jobs , Operations1 can have further bifurcation into MINI operation ie Jobs. like QTB (Example Bringing Paint on Floor), Setup (Mixing Red with Blue Color), Process, Transport.
- Activation Button - if its marked yes that means it will take the cost for that Job type only from cost categories (for Setup and Process we will define cost under cost categories).
- Working time - it will not on Saturday and Sunday as you have mentioned on Calendar. Capacity - Route will use the mentioned capacity on calendar (Like 5 hrs or 24 hrs) and it will not use infinite Capacity
- Estimation and Costing - at the time of Production Order , we do click on Estimate at that time system will calculate the cost that is defined here on Route and also from Raw material and then both amount will be sums as estimate Cost.
- Estimation is related to Cost categories - for Setup, Runtime and Process Qty Further in this page we will setup the cost .
- Either enable Boolean - "Setup and Runtime" or Only Qty option here because it will double the cost, Qty will multiple with Hours = 7*5(Hous) = $35 or Setup cost ($5)+Runtime($5) = 10* 7= 70 (Desired Qty). if we enable all then it will come as $35+70 =$105 (that will be incorrect)
- Automatic route consumption is just like flushing principle - Options like Always, Never and Automatic if its automatic that means Raw material will be consumed automatically. Please note - this is Discrete Route group we can have Process route group too.
- Now all the setup has done but from where we are going to take the cost for this operation . for that only we create Cost categories. Before cost categories we have to create Shared categories.
- Shared Categories : it will tell us the module use (be it Production or Project). When ever you need to set a new price, you can setup a new shared categories. for Example - if you want your Cutting price needs to be different then Car Speaker Assembly price. They allow categories to be shared across all legal entities
and modules of a company. This functionality becomes useful when employees of
another legal entity work on projects for another legal entity.
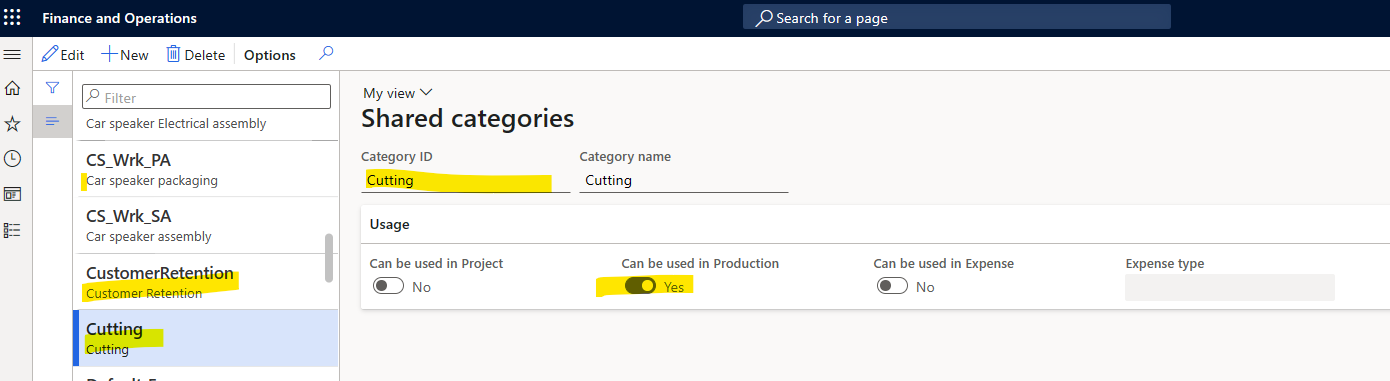
- Cost Categories : Here you will define the cost and tag this to Shared categories then click on categories setup for costing version and pick one then Tag one Cost group. (Costing version I have explain in another Blog).Cost categories apply to manufacturing environments that use routing. The cost groups that are assigned to cost categories classify manufacturing cost contributions, based on the operation resources and the type of activity, such as setup time and run time.
- Cost Group : Group is basically different type like Direct manufacturing, Indirect manufacturing, Direct Outsourcing etc.it Can also have profit % , so if you remember on Production order , that calculate the estimate production Price , it can also calculate the Estimated Sales Price if you are giving some % on Profit %.
- Resource Requirement : Now who is going to perform all above setup, its a Machine or a Human, For that only we need to create Resource. Resource group is a combination of Both (Machine and Human). if you are selecting Resource group the system will pick any available resources for that particular Day. Create resource group and add calendar & Resource (Man or Machine) and enable Finite Capacity, also define the relevant ledger posting account.
- Resource : It can be Human or Machine. If you are creating resource as Human then system will ask you to tag worker.
- Summary : if you have mentioned all Information on Operations relations ( ie on operation relations - be is Setup, runtime , Cost group , resources, etc then again you don't have to add any thing on route).
Routes Creations :
Route:
A route defines the structure of the production process. In other words, it
defines the order of operations.
- Create Route: A route describes the order of operations that is used to produce a product or product variant. (Mentioned below).
- Route version: Here you can create different route version –
i.e., Based on Different site 2 or 3, from different date range 2/2- 22/5/2023
for Qty 50 or 60. (So if you have order for more than 50 Qty for site 2 then this
route version will be picked)
- Operations: An
operation is a step in the production process. Assembly,Cutting etc .
- Run Time : what amount of time will above operation take to produce this process Qty. Example 8 hours
- Process Qty : Total Qty that will be produced after the operation based on Run time. Example 20 Qty
- Next = if the Value is 0 that means we are ending the operation but if its more then 1 then the new Operation will be there to produce the Goods.
- Route Group : Every operation can be further broken down into Jobs , Operations1 can have further bifurcation into MINI operation ie Jobs. like QTB (Example Bringing Paint on Floor), Setup (Mixing Red with Blue Color), Process, Transport.
- Activation Button - if its marked yes that means it will take the cost for that Job type only from cost categories (for Setup and Process we will define cost under cost categories).
- Working time - it will not on Saturday and Sunday as you have mentioned on Calendar. Capacity - Route will use the mentioned capacity on calendar (Like 5 hrs or 24 hrs) and it will not use infinite Capacity
- Estimation and Costing - at the time of Production Order , we do click on Estimate at that time system will calculate the cost that is defined here on Route and also from Raw material and then both amount will be sums as estimate Cost.
- Estimation is related to Cost categories - for Setup, Runtime and Process Qty Further in this page we will setup the cost .
- Either enable Boolean - "Setup and Runtime" or Only Qty option here because it will double the cost, Qty will multiple with Hours = 7*5(Hous) = $35 or Setup cost ($5)+Runtime($5) = 10* 7= 70 (Desired Qty). if we enable all then it will come as $35+70 =$105 (that will be incorrect)
- Automatic route consumption is just like flushing principle - Options like Always, Never and Automatic if its automatic that means Raw material will be consumed automatically. Please note - this is Discrete Route group we can have Process route group too.
- Now all the setup has done but from where we are going to take the cost for this operation . for that only we create Cost categories. Before cost categories we have to create Shared categories.
- Shared Categories : it will tell us the module use (be it Production or Project). When ever you need to set a new price, you can setup a new shared categories. for Example - if you want your Cutting price needs to be different then Car Speaker Assembly price. They allow categories to be shared across all legal entities
and modules of a company. This functionality becomes useful when employees of
another legal entity work on projects for another legal entity.
- Cost Categories : Here you will define the cost and tag this to Shared categories then click on categories setup for costing version and pick one then Tag one Cost group. (Costing version I have explain in another Blog).Cost categories apply to manufacturing environments that use routing. The cost groups that are assigned to cost categories classify manufacturing cost contributions, based on the operation resources and the type of activity, such as setup time and run time.
- Cost Group : Group is basically different type like Direct manufacturing, Indirect manufacturing, Direct Outsourcing etc.it Can also have profit % , so if you remember on Production order , that calculate the estimate production Price , it can also calculate the Estimated Sales Price if you are giving some % on Profit %.
- Resource Requirement : Now who is going to perform all above setup, its a Machine or a Human, For that only we need to create Resource. Resource group is a combination of Both (Machine and Human). if you are selecting Resource group the system will pick any available resources for that particular Day. Create resource group and add calendar & Resource (Man or Machine) and enable Finite Capacity, also define the relevant ledger posting account.
- Resource : It can be Human or Machine. If you are creating resource as Human then system will ask you to tag worker.
- Summary : if you have mentioned all Information on Operations relations ( ie on operation relations - be is Setup, runtime , Cost group , resources, etc then again you don't have to add any thing on route).
L Lets create Operation :
Lets create route group
Overview Tab
L Lets setup Shared categories
Lets setup Cost categories
Categories Setup
Cost Groups- for Setup
Updated Results
Cost Groups- for Assembly
After create, estimate, clicked on Start with highlighted points.
Route Card.
Comments